Существует несколько методов изготовления гнутых деревянных изделий, которые полностью отличаются друг от друга.
Первый метод заключается в вырезании из цельного куска древесины по необходимому контуру согласно шаблону деревянного элемента. При кажущейся простоте этот метод имеет существенные недостатки. Древесина, имеющая прямые волокна, в местах изгибов может раскалываться вдоль волокон, что существенно сказывается на прочности изготовленного изделия в целом. Кроме этого данная технология влечет за собой повышенный расход древесины.
Второй метод, используемый уже много столетий, состоит в размягчении деревянных изделий посредством кипячения или пропаривания в металлических формах. Для этого деревянную заготовку помещают в емкость с кипящей водой и выдерживают несколько часов, поддерживая кипение воды. После этого в местах изгибов создается механическое напряжение для придания конструкции необходимой формы. Для этого применяются всевозможные приспособления, напоминающие трубогибочные станки. Изогнутый элемент фиксируют в таком положении до полного его высыхания. После просушивания изгиб остается при снятых фиксаторах. Волокна древесины, изогнутой таким образом, принимают форму элемента и его физико-механические свойства практически не отличаются от прямого куска древесины. Если необходимо изготавливать несколько одинаковых гнутых элементов (тетивы лестницы или поручни), для соблюдения идентичности следует «гнутье» выполнять в специально для этой цели изготовленных кондукторах. В противном случае добиться полной идентичности будет сложно.
Третий метод заключается в наклеивании на деревянный брусок тонких полосок древесины в местах, соответствующих выпуклой части элемента. Многослойное наклеивание с последующей механической обработкой позволяет придать деревянному элементу любые, даже самые затейливые, формы. Этот метод довольно трудоемок и длителен, особенно в условиях домашних мастерских.
Современные технологии позволяют получить деревянные клееные конструкции (ДКК) любой формы и длины. Состоят они обычно из двух и более слоев пиломатериалов, склеенных между собой таким образом, чтобы волокна всех слоев были абсолютно или приблизительно параллельны (рис. 1).
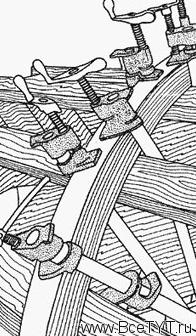
Рис. 1. Изготовление изогнутых деталей
Для изготовления ДКК чаще всего используют сосну или ель. При необходимости получить текстуру ценных пород древесины прибегают к шпонированию или фанерованию. При изготовлении ДКК пиломатериалы максимальной толщины идут для прямолинейных участков или криволинейных с радиусом кривизны 6 м и более. Для всех других криволинейных элементов толщина пиломатериалов не должна превышать 1/50 радиусов их кривизны. Очень важным моментом технологии изготовления ДКК является сушка материалов. Она в значительной степени определяет эксплуатационную прочность гнутого элемента. Во избежание появления в элементах внутренних напряжений очень важно, чтобы склеиваемые слои имели одинаковую влажность или чтобы разница по влажности слоев не превышала 5%. При этом современные технологии располагают методиками сушки, рассмотренными нами ранее. Лестницы, изготовленные из элементов ДКК, по своим физико-механическим и эстетическим качествам не уступают, а по многим параметрам превосходят изделия, выполненные из цельной древесины.